Research + Development
Sample projects of test rigs and other product development activities.
Medical Device Test Rig
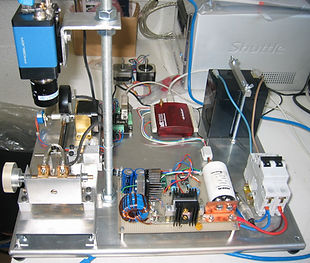
Commissioned by the Client, NeedleSmart to design, construct and develop a low cost, proof of concept test rig for a process to safely destroy medical hypodermic needles and so minimise serious needlestick injuries for all medical professionals
Design and construction of a novel breadboard level high current power supply, auxiliary control board and stepper motor drive together with integration into the test rig.
The test rig was controlled using a custom designed National Instruments LabVIEW software program which provided the user interface, high speed video event capture and comprehensive data logging capabilities.
The test rig achieved the proof of concept requirements for the Client, world wide patents have been granted and the device is close to mass production.
Follow on design of the circuit board hardware of a 3 phase high current synchronous buck power converter for the prototype devices based on a high speed PIC microcontroller.
Assistance provided to enable the prototype devices to pass the relevant European EMC tests at a certified test facility.

DC Drive Power Board
Development of a power circuit board for a wide range of DC thyristor regenerative converter variable speed drives.
Provided all line current and high voltage feedback measurements, together with the isolated thyristor firing currents to allow the drive to operate.
Also provided the design for an off-line switched mode power supply to supply all drive functions.
Entered full production with many thousands manufactured during the product lifespan.
Ultrasonic Measurement Sensor
Design and development of a prototype microprocessor controlled ultrasonic distance measurement sensor. Included all hardware design at breadboard level together with microprocessor assembler code for all sensor functions.


Maglev Research Project
Post graduate research into the design and control of a new type of linear homopolar synchronous motor for the lift and propulsion of a maglev light rail vehicle.
Construction of a dynamometer test rig with the passive rail in the form of a wheel, together with a floating force measurement platform to support the small scale motor. This simulated one 2 phase motor which would be used as lift and propulsion for a single corner of the light rail vehicle.
Computer modelling of the motor, airgap control system and propulsion inverter drive.
Successfully lifted 200kg of mass at a controlled air gap and provided propulsion forces to rotate the rail "wheel" equivalent to the required vehicle acceleration.